పెట్టుబడి కాస్టింగ్ యొక్క డైమెన్షనల్ స్థిరత్వాన్ని ప్రభావితం చేసే వివిధ అంశాలు
పెట్టుబడి కాస్టింగ్ల యొక్క డైమెన్షనల్ ఖచ్చితత్వాన్ని నిరంతరం మెరుగుపరచడం మరియు అధిక పరిమాణం వల్ల కలిగే వ్యర్థ ఉత్పత్తులను తగ్గించడం ఎల్లప్పుడూ దేశీయ మరియు విదేశాలలో పెట్టుబడి కాస్టింగ్ కార్మికులు అనుసరించే ప్రధాన లక్ష్యాలలో ఒకటి.
1. పెట్టుబడి కాస్టింగ్ల డైమెన్షనల్ స్థిరత్వం
1. మైనపు నమూనా యొక్క డైమెన్షనల్ స్థిరత్వం మరియు దాని ప్రభావ కారకాలు
చాలా సందర్భాలలో, కాస్టింగ్ పరిమాణం హెచ్చుతగ్గులకు గురైనప్పుడు మైనపు అచ్చు పరిమాణం బాగా హెచ్చుతగ్గులకు లోనవుతుంది మరియు కొన్ని మినహాయింపులు ఉన్నాయి. మొత్తంమీద, మైనపు అచ్చు యొక్క పరిమాణ హెచ్చుతగ్గులు కాస్టింగ్ యొక్క పరిమాణ హెచ్చుతగ్గులలో 10% నుండి 70% వరకు ఉంటాయి.
అచ్చు ప్రక్రియ పారామితులు మైనపు అచ్చు యొక్క డైమెన్షనల్ స్థిరత్వంపై నిర్ణయాత్మక ప్రభావాన్ని కలిగి ఉంటాయి. ప్రధాన కారకాలు క్రింది విధంగా ఉన్నాయి:
(1) మైనపు నొక్కడం ఉష్ణోగ్రత
మైనపు నొక్కిన ఉష్ణోగ్రత ప్రభావం కారణంగా వివిధ మౌల్డింగ్ పదార్థాలు వేర్వేరు ప్రదర్శనలను కలిగి ఉంటాయి. మైనపు ఆధారిత మౌల్డింగ్ మెటీరియల్స్ ఉపయోగించినప్పుడు, మైనపు ఒత్తిడి ఉష్ణోగ్రత మైనపు అచ్చు డైమెన్షనల్ స్టెబిలిటీ ప్రభావానికి చాలా సున్నితంగా ఉంటుంది, అయితే రెసిన్ ఆధారిత మౌల్డింగ్ మెటీరియల్స్ తక్కువ ప్రభావాన్ని కలిగి ఉంటాయి.
(2) ఇంజెక్షన్ ఒత్తిడి
ఒత్తిడి చిన్నగా ఉన్నప్పుడు, ఒత్తిడి పెరిగినప్పుడు మైనపు అచ్చు యొక్క సంకోచం రేటు గణనీయంగా తగ్గుతుంది. అయితే, ఒత్తిడి కొంత మేరకు (≥1.6MPa) పెరిగిన తర్వాత, మైనపు అచ్చు పరిమాణంపై ఒత్తిడి దాదాపుగా ప్రభావం చూపదు. విదేశీ పరీక్ష ఫలితాలు తరచుగా "మైనపు అచ్చు పరిమాణంతో ఒత్తిడికి ఎలాంటి సంబంధం లేదు" అని నిర్ధారించడంలో ఆశ్చర్యం లేదు, కానీ అనేక దేశీయ కంపెనీల అభిప్రాయం పూర్తిగా ఒకేలా ఉండదు.
(3) ప్రవాహం రేటు
అచ్చు పదార్థం యొక్క ప్రవాహం రేటు క్రింది రెండు విధాలుగా మార్చవచ్చు, కానీ మైనపు అచ్చు పరిమాణంపై ప్రభావం ఒకేలా ఉండదు:
Wa మైనపు ప్రెస్ యొక్క ఫ్లో స్పీడ్ సెట్టింగ్ని మార్చడం ద్వారా, ఈ పద్ధతి మైనపు అచ్చు యొక్క సంకోచంపై తక్కువ ప్రభావం చూపుతుంది. ఏదేమైనా, సంక్లిష్ట ఆకృతులతో సన్నని గోడల భాగాల పూరకం మరియు ఉపరితల నాణ్యతపై లేదా కోర్లతో మైనపు అచ్చులపై ఇది ముఖ్యమైన ప్రభావాన్ని కలిగి ఉంటుంది.
· మైనపు ఇంజెక్షన్ పోర్ట్ యొక్క క్రాస్ సెక్షనల్ ప్రాంతాన్ని మార్చడం ద్వారా ఈ పద్ధతి గొప్ప ప్రభావాన్ని కలిగి ఉంటుంది, ఎందుకంటే మైనపు ఇంజెక్షన్ పోర్ట్ యొక్క క్రాస్ సెక్షనల్ ప్రాంతాన్ని పెంచడం వల్ల మైనపు నొక్కే ఉష్ణోగ్రతను తగ్గించడమే కాకుండా, ఘనీభవనాన్ని పొడిగించవచ్చు మైనపు ఇంజెక్షన్ పోర్ట్ వద్ద అచ్చు పదార్థం యొక్క సమయం, తద్వారా మైనపు అచ్చు సంపీడనం పెరుగుతుంది, సంకోచం మరియు ఉపరితల సంకోచం యొక్క డిగ్రీ తగ్గుతుంది.
(4) ఇంజెక్షన్ సమయం
ఇక్కడ పిలవబడే ఇంజెక్షన్ సమయం నింపడం, కాంపాక్ట్ చేయడం మరియు నిర్వహించడం అనే మూడు కాలాలను కలిగి ఉంటుంది. పూరక సమయం అచ్చు కుహరాన్ని పూరించడానికి అచ్చు పదార్థం యొక్క సమయాన్ని సూచిస్తుంది; సంపీడనం అచ్చును పూరించడం నుండి మైనపు ఇంజెక్షన్ ముక్కు మూసివేసే వరకు సమయాన్ని సూచిస్తుంది; మరియు హోల్డింగ్ అనేది మైనపు ఇంజెక్షన్ ముక్కు నుండి అచ్చు యొక్క ఎజెక్షన్ వరకు మూసివేసే సమయాన్ని సూచిస్తుంది.
మైనపు అచ్చు యొక్క సంకోచం రేటుపై ఇంజెక్షన్ సమయం గణనీయమైన ప్రభావాన్ని చూపుతుంది. ఎందుకంటే ఇంజెక్షన్ సమయాన్ని పెంచడం ద్వారా మరింత అచ్చు పదార్థం కుహరంలోకి దూరి ఉండవచ్చు, మరియు మైనపు అచ్చు మరింత కుదించబడుతుంది, తద్వారా సంకోచం రేటు తగ్గుతుంది. సుదీర్ఘమైన సంపీడన సమయంతో మైనపు మోడల్ బరువు పెరుగుతుంది. సంపీడన సమయం తగినదిగా ఉండాలి. సంపీడన సమయం చాలా పొడవుగా ఉంటే, మైనపు ఇంజెక్షన్ పోర్ట్ వద్ద అచ్చు పదార్థం పూర్తిగా పటిష్టం చేయబడింది మరియు సంపీడనం పనిచేయదు. ఇంజెక్షన్ సమయం తక్కువగా ఉన్నప్పుడు (4-15 సె), మైనపు నొక్కే ఉష్ణోగ్రత పెరుగుతుంది మరియు సంకోచం రేటు పెరుగుతుంది అని మూర్తి 25 నుండి కూడా చూడవచ్చు; కానీ ఇంజెక్షన్ సమయం 25-35 సెకన్లకు పొడిగించబడినప్పుడు (ఫిల్లింగ్ సమయం స్థిరంగా ఉంటుందనే భావనతో, పైన పేర్కొన్నది సంపీడన సమయాన్ని పొడిగించడం) మైనపు నొక్కిన ఉష్ణోగ్రత ప్రభావం చిన్నదిగా మారుతుంది; ఇంజెక్షన్ సమయం 35 సెకన్ల కంటే ఎక్కువ పెరిగినప్పుడు, వ్యతిరేక పరిస్థితి ఏర్పడుతుంది, అనగా మైనపు నొక్కిన ఉష్ణోగ్రత పెరిగినప్పుడు, మైనపు అచ్చు సంకోచం రేటు బదులుగా తగ్గుతుంది. ఈ దృగ్విషయాన్ని అచ్చు పదార్థ ఉష్ణోగ్రతను పెంచడం మరియు సంపీడన సమయాన్ని పొడిగించడం వలన మైనపు అచ్చు సంపీడనం యొక్క డిగ్రీని పెంచే ప్రభావం ఉంటుంది.
(5) అచ్చు ఉష్ణోగ్రత మరియు మైనపు నొక్కడం పరికరాలు
అచ్చు ఉష్ణోగ్రత ఎక్కువగా ఉంటుంది, మైనపు అచ్చు నెమ్మదిగా చల్లబడుతుంది మరియు సంకోచం రేటు పెరుగుతుంది. అచ్చు బయటకు పోవడానికి ముందు మైనపు అచ్చు ఇప్పటికీ కంప్రెషన్ మౌల్డింగ్లో ఉంది, మరియు సంకోచం పరిమితంగా ఉంటుంది, కానీ అచ్చును తొలగించిన తర్వాత, అది ముడుచుకోవడానికి స్వేచ్ఛగా మారుతుంది. అందువల్ల, అచ్చు విడుదలైనప్పుడు మైనపు అచ్చు ఉష్ణోగ్రత ఎక్కువగా ఉంటే, తుది సంకోచం రేటు పెద్దదిగా ఉంటుంది మరియు దీనికి విరుద్ధంగా, సంకోచం రేటు చిన్నదిగా ఉంటుంది.
అదే విధంగా, మైనపు ప్రెస్ యొక్క శీతలీకరణ వ్యవస్థ మైనపు అచ్చు పరిమాణంపై 0.3% ప్రభావాన్ని కలిగి ఉండవచ్చు.
చివరగా, మైనపు ఆధారిత అచ్చు పదార్థాలను ఉపయోగించినప్పుడు, మైనపు పేస్ట్ అనేది ఘన, ద్రవ మరియు వాయువు యొక్క మూడు దశల సహజీవన వ్యవస్థ అని నొక్కి చెప్పడం విలువ. మూడు దశల మధ్య వాల్యూమ్ నిష్పత్తి మైనపు అచ్చు పరిమాణంపై గొప్ప ప్రభావాన్ని చూపుతుంది. ఈ మూడింటి మధ్య అనుపాత సంబంధాన్ని వాస్తవ ఉత్పత్తిలో నియంత్రించలేము, మైనపు ఆధారిత అచ్చు పదార్థాలను ఉపయోగించి మైనపు అచ్చుల పేలవమైన డైమెన్షనల్ స్థిరత్వానికి ఇది కూడా ఒక ముఖ్యమైన కారణం.
2. కాస్టింగ్ల డైమెన్షనల్ స్టెబిలిటీపై షెల్ మెటీరియల్ మరియు షెల్ మేకింగ్ ప్రాసెస్ ప్రభావం
కాస్టింగ్ పరిమాణంపై అచ్చు షెల్ ప్రభావం ప్రధానంగా కాల్పుల సమయంలో అచ్చు షెల్ యొక్క ఉష్ణ విస్తరణ మరియు ఉష్ణ వైకల్యం (అధిక ఉష్ణోగ్రత క్రీప్) మరియు శీతలీకరణ సంకోచంపై అచ్చు షెల్ యొక్క పరిమితి (అడ్డంకి) వలన కలుగుతుంది. కాస్టింగ్.
(1) షెల్ యొక్క థర్మల్ విస్తరణ
ప్రధానంగా షెల్ మెటీరియల్పై ఆధారపడి ఉంటుంది. వివిధ వక్రీభవన పదార్థాలు వేర్వేరు విస్తరణ రేట్లను కలిగి ఉంటాయి. సాధారణంగా ఉపయోగించే వక్రీభవనాలలో, ఫ్యూజ్డ్ సిలికా అతిచిన్న విస్తరణ రేటును కలిగి ఉంది, తరువాత అల్యూమినియం సిలికేట్, మరియు సిలికా అతిపెద్దది మరియు అసమానమైనది. పరీక్షించిన తరువాత, అల్యూమినియం సిలికేట్ షెల్ను గది ఉష్ణోగ్రత నుండి 1000 to వరకు వేడి చేయవచ్చని నిర్ణయించబడుతుంది, షెల్ 0.25% విస్తరణను ఉత్పత్తి చేయగలదు, ఇది కాస్టింగ్ పరిమాణం యొక్క మొత్తం సంకోచం యొక్క చిన్న నిష్పత్తిని కలిగి ఉంటుంది. అందువల్ల, అటువంటి వక్రీభవన పదార్థాలను ఉపయోగించినట్లయితే, షెల్ ఇది మెరుగైన డైమెన్షనల్ స్టెబిలిటీని కలిగి ఉంటుంది, ఫ్యూజ్డ్ సిలికా వంటివి నిస్సందేహంగా మెరుగ్గా ఉంటాయి. అయితే, సిలికాను ఉపయోగించినట్లయితే, షెల్ పరిమాణం బాగా హెచ్చుతగ్గులకు లోనవుతుంది.
(2) ఉష్ణ వైకల్యం (అధిక ఉష్ణోగ్రత క్రీప్)
ఉదాహరణకు, సిలికా సోల్ మరియు ఇథైల్ సిలికేట్ షెల్స్ కంటే 1000 ° C కంటే ఎక్కువ ఉష్ణోగ్రత వద్ద వాటర్ గ్లాస్ను బైండర్గా ఉపయోగించే షెల్ గణనీయంగా ఎక్కువ క్రీప్ డిగ్రీని కలిగి ఉంటుంది. ఫ్యూజ్డ్ కోరండమ్లో అధిక వక్రీభవనత ఉన్నప్పటికీ, సోడియం ఆక్సైడ్ వంటి మలినాలు ఉండటం వలన, షెల్ ఫైరింగ్ ఉష్ణోగ్రత 1000 higher కంటే ఎక్కువగా ఉండటం వల్ల కూడా క్రీప్ ఏర్పడవచ్చు, ఫలితంగా పేలవమైన డైమెన్షనల్ స్టెబిలిటీ ఏర్పడుతుంది.
(3) కాస్టింగ్ యొక్క సంకోచంపై అచ్చు షెల్ యొక్క నిర్బంధం -అచ్చు షెల్ యొక్క తిరోగమనం మరియు కూలిపోయే అవకాశం ఇది కూడా ప్రధానంగా అచ్చు షెల్ యొక్క పదార్థంపై ఆధారపడి ఉంటుంది.
సారాంశంలో, కాస్టింగ్ యొక్క పరిమాణ హెచ్చుతగ్గులపై షెల్ ప్రభావంలో వక్రీభవన పదార్థాలు ప్రధాన పాత్ర పోషిస్తాయి, అయితే బైండర్ పాత్రను విస్మరించలేము. దీనికి విరుద్ధంగా, షెల్ తయారీ ప్రక్రియ యొక్క ప్రభావం చిన్నది.
3. డైమెన్షనల్ స్టెబిలిటీపై కాస్టింగ్ల అసమాన శీతలీకరణ వలన కలిగే ఒత్తిడి ప్రభావం
కాస్టింగ్ యొక్క ప్రతి భాగం యొక్క శీతలీకరణ రేటు (గేటింగ్ సిస్టమ్తో సహా) భిన్నంగా ఉంటుంది, ఇది ఉష్ణ ఒత్తిడిని సృష్టిస్తుంది మరియు కాస్టింగ్ను వైకల్యం చేస్తుంది, తద్వారా డైమెన్షనల్ స్టెబిలిటీని ప్రభావితం చేస్తుంది. వాస్తవ ఉత్పత్తిలో ఇది తరచుగా ఎదురవుతుంది. కాస్టింగ్ల శీతలీకరణ రేటును తగ్గించడం మరియు రన్నర్ల కలయికను మెరుగుపరచడం ప్రభావవంతమైన నివారణ చర్యలు.
2. ఖచ్చితత్వం-అచ్చు సంకోచం రేటు మెరుగుపరచడానికి కీ సరిగ్గా కేటాయించబడింది
పైన పేర్కొన్న "డైమెన్షనల్ స్టెబిలిటీ" "డైమెన్షనల్ ఖచ్చితత్వం" మరియు "ఖచ్చితత్వం (ఖచ్చితత్వం)" కి భిన్నంగా ఉంటుంది. డైమెన్షనల్ స్టెబిలిటీ (అంటే ఖచ్చితత్వం) డైమెన్షనల్ స్థిరత్వానికి పర్యాయపదంగా ఉంటుంది, డైమెన్షనల్ హెచ్చుతగ్గులు లేదా చెదరగొట్టే స్థాయిని ప్రతిబింబిస్తుంది మరియు సాధారణంగా ప్రామాణిక విచలనం ద్వారా కొలుస్తారు. డైమెన్షనల్ అస్థిరతకు ప్రధాన కారణం లాక్స్ ప్రాసెస్ కంట్రోల్, ఇది యాదృచ్ఛిక లోపం. ఖచ్చితత్వం అనేది కాస్టింగ్లో నిర్దిష్ట పరిమాణానికి, అంటే సగటు విచలనం యొక్క పరిమాణానికి నామమాత్ర పరిమాణం నుండి అనేక కొలిచిన విలువల యొక్క అంకగణిత సగటు స్థాయిని సూచిస్తుంది. పెట్టుబడి కాస్టింగ్ కోసం, పేలవమైన డైమెన్షనల్ ఖచ్చితత్వానికి ప్రధాన కారణం ప్రొఫైలింగ్ డిజైన్ సమయంలో సంకోచం రేటు సరిగా కేటాయించకపోవడమే, ఇది ఒక క్రమబద్ధమైన లోపం, ఇది సాధారణంగా అచ్చును పదేపదే రిపేర్ చేయడం ద్వారా సర్దుబాటు చేయబడుతుంది. డైమెన్షనల్ ఖచ్చితత్వం (ఖచ్చితత్వం) పై రెండింటి కలయిక. అందువల్ల, కాస్టింగ్ల డైమెన్షనల్ ఖచ్చితత్వాన్ని మెరుగుపరచడానికి మరియు ఉత్పత్తి సైజు టాలరెన్స్ల సమస్యను పరిష్కరించడానికి, డైమెన్షనల్ హెచ్చుతగ్గులను తగ్గించడానికి ప్రక్రియను ఖచ్చితంగా నియంత్రించడమే కాకుండా, ప్రొఫైల్ రూపకల్పన చేసేటప్పుడు కాస్టింగ్ యొక్క ప్రతి డైమెన్షన్ యొక్క సంకోచం రేటును సరిగ్గా కేటాయించాలి .
ఖచ్చితమైన కాస్టింగ్ల తుది మొత్తం సంకోచం మైనపు అచ్చు, మిశ్రమం సంకోచం మరియు చిన్న మొత్తంలో షెల్ విస్తరణ కలయిక అని అందరికీ తెలుసు. షెల్ 0.25%వరకు ఉబ్బుతుంది మరియు దాని ప్రభావం పరిమితం. మిశ్రమం యొక్క సరళ సంకోచం రేటు తరచుగా మైనపు అచ్చు కంటే ఎక్కువగా ఉన్నప్పటికీ, మైనపు నొక్కడం ప్రక్రియ వలన డైమెన్షనల్ హెచ్చుతగ్గులు ఎక్కువ ప్రభావాన్ని చూపుతాయి. అచ్చు మరమ్మత్తు ఖర్చు తగ్గించడానికి మరియు కాస్టింగ్ సైజు హెచ్చుతగ్గులను తగ్గించడానికి, మైనపు అచ్చు యొక్క సంకోచం రేటును నియంత్రించడం చాలా ముఖ్యం.
1. మైనపు అచ్చు సంకోచం
మైనపు అచ్చు పరిమాణాన్ని పూర్తిగా స్థిరీకరించిన తర్వాత మైనపు అచ్చు యొక్క సంకోచాన్ని కొలవాలి. ఎందుకంటే అచ్చును బయటకు తీసిన తర్వాత మైనపు అచ్చు సంకోచం పూర్తిగా ఆగదు. మైనపు అచ్చు యొక్క పరిమాణం కొన్నిసార్లు అచ్చును తొలగించిన కొన్ని రోజుల తర్వాత మాత్రమే స్థిరీకరిస్తుంది. ఏదేమైనా, అచ్చు పదార్ధం యొక్క సంకోచం చాలావరకు అచ్చును బయటకు తీసిన తర్వాత ఒకటి నుండి అనేక గంటలలోపు పూర్తి చేయబడుతుంది. మైనపు అచ్చు సంకోచం రేటు ప్రధానంగా క్రింది ప్రభావిత కారకాలను కలిగి ఉంది:
(1) అచ్చు పదార్థం రకం;
(2) మైనపు మోడల్ యొక్క విభాగ పరిమాణం;
మైనపు అచ్చు యొక్క క్రాస్ సెక్షనల్ పరిమాణం సంకోచం రేటుపై గణనీయమైన ప్రభావాన్ని చూపుతుందని నొక్కి చెప్పడం విలువ. ఉదాహరణకు, వివిధ మందం కలిగిన మైనపు అచ్చులను నొక్కినప్పుడు సాధారణ పూరించని అచ్చు పదార్థం యొక్క సంకోచం రేటు. మైనపు అచ్చు యొక్క విభాగం యొక్క మందం సాధారణంగా 13 మిమీ మించకూడదు. మందం 13 మిమీ కంటే ఎక్కువగా ఉన్నప్పుడు, సంకోచాన్ని తగ్గించే ఉద్దేశ్యాన్ని సాధించడానికి కోల్డ్ మైనపు బ్లాక్స్ లేదా మెటల్ కోర్లను ఉపయోగించడం ద్వారా గోడ మందం తగ్గించవచ్చు, ఇది ఫిల్లర్ కాని అచ్చు పదార్థాలకు చాలా ముఖ్యం.
గమనిక: 1. నీటిలో కరిగే అచ్చు పదార్థం యొక్క సంకోచం రేటు సుమారు 0.25%;
2. కరిగే కోర్లు, సిరామిక్ కోర్లు లేదా క్వార్ట్జ్ గ్లాస్ ట్యూబ్లను ఉపయోగిస్తున్నప్పుడు, కోర్తో సంబంధంలో మైనపు అచ్చు యొక్క సరళ సంకోచం ఉండదు;
(3) కోర్ రకాలు
మైనపు అచ్చు యొక్క కుహరం పరిమాణం నిస్సందేహంగా కోర్ ఆకృతికి అనుగుణంగా ఉంటుంది. అందువల్ల, మైనపు అచ్చు యొక్క కుహరం యొక్క డైమెన్షనల్ ఖచ్చితత్వాన్ని మెరుగుపరచడానికి కోర్ల ఉపయోగం ఒక మార్గంగా మారింది.
2. మిశ్రమం సంకోచం
మిశ్రమం సంకోచం ప్రధానంగా కింది అంశాలపై ఆధారపడి ఉంటుంది:
Ast తారాగణం మిశ్రమం రకం మరియు రసాయన కూర్పు;
Ge ప్రసార జ్యామితి (పరిమితి స్థితి మరియు విభాగం పరిమాణంతో సహా);
Pour కాస్టింగ్ పారామితులు, పోయడం ఉష్ణోగ్రత, షెల్ ఉష్ణోగ్రత, కాస్టింగ్ కూలింగ్ రేట్ మొదలైనవి;
C సిరామిక్ కోర్లు, క్వార్ట్జ్ గ్లాస్ ట్యూబ్లు మొదలైనవి ఉపయోగించడం.
పోయడం ఉష్ణోగ్రత, షెల్ ఉష్ణోగ్రత, కాస్టింగ్ కూలింగ్ రేట్ మరియు ఇతర ప్రాసెస్ పారామితులు సాధారణంగా ప్రొడక్షన్ ప్రాసెస్ సమయంలో ప్రామాణిక ప్రాసెస్ కార్డ్ల ద్వారా ఖచ్చితంగా నియంత్రించబడతాయి, దీని వలన కలిగే సైజు హెచ్చుతగ్గులు వేర్వేరు ప్రొడక్షన్ బ్యాచ్ల మధ్య పెద్దగా ఉండవు. పోసే ఉష్ణోగ్రత ప్రాసెస్ స్పెసిఫికేషన్ ద్వారా అవసరమైన పరిధిని మించినప్పటికీ, కాస్టింగ్ సైజు హెచ్చుతగ్గులు సాధారణంగా పెద్దవి కావు. మైనపు అచ్చు మాదిరిగానే, కాస్టింగ్ యొక్క విభాగం పరిమాణం మరియు అచ్చు షెల్ యొక్క అడ్డంకులు మిశ్రమం యొక్క సంకోచాన్ని ప్రభావితం చేసే ప్రధాన కారకాలు. పూర్తిగా సంకోచించబడిన పరిమాణం యొక్క సంకోచం రేటు ఉచిత సంకోచం రేటులో 85% నుండి 89% వరకు ఉందని అనుభవం చూపిస్తుంది; సెమీ-నిర్బంధ పరిమాణం 94% నుండి 95% వరకు ఉంటుంది.
3. కొలత కోసం మొదటి బ్యాచ్ నమూనాల కనీస సంఖ్య
పైన జాబితా చేయబడిన సంకోచం రేటు గత అనుభవం ఆధారంగా అనుభావిక డేటా, నిజమైన సంకోచం రేటు కాదు. ఈ డేటా ప్రకారం అచ్చుల రూపకల్పన మరియు తయారీ, మరమ్మత్తు అనివార్యం. మరమ్మతుల ఖచ్చితత్వం మరియు విజయాల రేటును మెరుగుపరచడానికి మరియు మరమ్మతుల సంఖ్యను తగ్గించడానికి, తగినంత సంఖ్యలో ట్రయల్ కాస్టింగ్ నమూనాల పరిమాణాన్ని జాగ్రత్తగా తనిఖీ చేయడం ఒక ముఖ్య లింక్. ఎందుకంటే మనం ఉత్పత్తి చేసే కాస్టింగ్ల పరిమాణం సరిగ్గా ఒకే విధంగా ఉండదు, కాబట్టి కొలిచిన నమూనాల సంఖ్య తగినంతగా ఉన్నప్పుడు మాత్రమే, పొందిన సగటు విలువ నిజమైన అంకగణిత సగటుకి దగ్గరగా ఉంటుంది. దీని నుండి, కనీస సంఖ్యలో కొలత నమూనాలు ఉత్పత్తి పరిమాణ స్థిరత్వాన్ని (ప్రాసెస్ సామర్ధ్యం) నియంత్రించడానికి ఉత్పత్తి ప్రక్రియ యొక్క ప్రక్రియ సామర్థ్యానికి నేరుగా సంబంధించినవి అని చూడటం కష్టం కాదు. కాస్టింగ్లు పరిమాణంలో పూర్తిగా ఒకేలా ఉంటే, పరీక్షించడానికి ఒక నమూనా మాత్రమే అవసరం; దీనికి విరుద్ధంగా, కాస్టింగ్ సైజు బాగా హెచ్చుతగ్గులకు గురైతే,
మరింత ఖచ్చితమైన సంకోచ డేటాను పొందడానికి చాలా నమూనాలను కొలవడం అవసరం. ముందు చెప్పినట్లుగా, పరిమాణాన్ని నియంత్రించే ఉత్పత్తి ప్రక్రియ యొక్క సామర్థ్యాన్ని ఈ ప్రక్రియ ద్వారా ఉత్పత్తి చేయబడిన కాస్టింగ్ పరిమాణం 6σ ద్వారా సూచించవచ్చు. చాలా పెట్టుబడి ఫౌండ్రీల ప్రస్తుత సాంకేతిక స్థాయి నుండి, Hp ఎక్కువగా 0.5 కంటే ఎక్కువగా ఉంటుంది, కాబట్టి మొదటి బ్యాచ్ కొలత నమూనాలకు సాధారణంగా కనీసం 11 నమూనాలు అవసరం.
మూడు. కొలత వ్యవస్థ విశ్లేషణ
ఉత్పత్తి పరిమాణ సమస్యలను విశ్లేషించేటప్పుడు మరియు పరిష్కరించేటప్పుడు, ఉపయోగించిన కొలత వ్యవస్థ యొక్క ఖచ్చితత్వం మరియు విశ్వసనీయతకు మేము శ్రద్ద ఉండాలి. కొలిచే సాధనాలు మరియు సామగ్రిని తరచుగా క్రమాంకనం చేయడంతో పాటు, కొలత లోపాలను తగ్గించడం కూడా చాలా ముఖ్యం. కొలత వ్యవస్థ (ఆపరేటర్ మరియు ఆపరేటింగ్ మెథడ్తో సహా) పెద్ద లోపం కలిగి ఉంటే, తిరస్కరించబడినవి అర్హత కలిగిన ఉత్పత్తులుగా మాత్రమే కాకుండా, అనేక అర్హత కలిగిన ఉత్పత్తులను తిరస్కరించబడినట్లుగా తప్పుగా అంచనా వేయవచ్చు, ఈ రెండూ పెద్ద ప్రమాదాలకు లేదా అనవసరమైన ఆర్థికానికి కారణం కావచ్చు నష్టాలు. నిర్దిష్ట కొలత పనికి కొలత వ్యవస్థ సరిపోతుందో లేదో తెలుసుకోవడానికి సులభమైన మార్గం పునరుత్పత్తి మరియు పునరావృత అర్హత పరీక్షలను నిర్వహించడం. రిపీటబిలిటీ అని పిలవబడేది అంటే, అదే ఇన్స్పెక్టర్ అదే భాగాన్ని తనిఖీ చేయడానికి మరియు ఫలితాల స్థిరత్వాన్ని పొందడానికి అదే ఇన్స్ట్రుమెంట్ (లేదా పరికరాలు) మరియు పద్ధతిని ఉపయోగిస్తాడు. పునరుత్పత్తి అనేది ఒకే భాగాన్ని తనిఖీ చేయడానికి వివిధ పరికరాలను ఉపయోగించి వేర్వేరు ఆపరేటర్లు పొందిన ఫలితాల స్థిరత్వాన్ని సూచిస్తుంది. అమెరికన్ ఆటోమోటివ్ ఇండస్ట్రీ యాక్షన్ గ్రూప్ (ఆటోమోటివ్ ఇండస్ట్రీ యాక్షన్ గ్రూప్) కొలవబడిన కాస్టింగ్ సైజు హెచ్చుతగ్గుల యొక్క ప్రామాణిక విచలనం యొక్క పునరావృతత మరియు పునరుత్పత్తి R & R యొక్క సమగ్ర ప్రామాణిక విచలనం కొలత వ్యవస్థకు ప్రమాణంగా ≤30% అవసరాలు [5]. కొన్ని పెద్ద-పరిమాణ మరియు సంక్లిష్ట ఆకారపు కాస్టింగ్ల కొలతలో, అన్ని కొలత వ్యవస్థలు ఈ అవసరాన్ని తీర్చలేవు. అచ్చులను కొలిచేటప్పుడు అనుమతించదగిన కొలత లోపం చిన్నదిగా ఉండాలి, సాధారణంగా 1/3.
నాలుగు. అచ్చు నిర్మాణం మరియు ప్రాసెసింగ్ స్థాయి
మైనపు అచ్చు పరిమాణం మరియు జ్యామితిపై అచ్చు నిర్మాణం మరియు ప్రాసెసింగ్ నాణ్యత ముఖ్యమైన ప్రభావాన్ని చూపుతాయని అందరికీ తెలుసు. ఉదాహరణకు, స్థానాలు మరియు బిగింపు యంత్రాంగం ఖచ్చితమైనది మరియు నమ్మదగినది అయినా, కదిలే భాగాల (కదిలే బ్లాక్స్, బోల్ట్లు మొదలైనవి) సరిపోలే క్లియరెన్స్ సముచితమైనదా, కాస్టింగ్ల డైమెన్షనల్ ఖచ్చితత్వాన్ని నిర్ధారించడానికి డ్రాయింగ్ పద్ధతి ప్రయోజనకరంగా ఉందా? , మొదలైనవి చెప్పనవసరం లేదు, గణనీయమైన సంఖ్యలో దేశీయ పెట్టుబడి కాస్టింగ్ ప్లాంట్ల కోసం, అచ్చు డిజైన్ మరియు తయారీ స్థాయిని అత్యవసరంగా మెరుగుపరచాలి.
ఫైవ్స్. ముగింపులో
పై విశ్లేషణ నుండి, పెట్టుబడి కాస్టింగ్ల డైమెన్షనల్ ఖచ్చితత్వాన్ని మెరుగుపరచడం అనేది ఇన్వెస్ట్మెంట్ కాస్టింగ్ ప్రొడక్షన్ ప్రాసెస్లోని అన్ని అంశాలతో కూడిన ఒక క్రమబద్ధమైన ప్రాజెక్ట్ అని చూడటం కష్టం కాదు. ప్రధాన అంశాలను ఈ క్రింది విధంగా సంగ్రహించవచ్చు:
1) అచ్చు ప్రక్రియ పారామితులను ఖచ్చితంగా నియంత్రించండి, ముఖ్యంగా కాస్టింగ్ పరిమాణంపై గణనీయమైన ప్రభావం చూపే పారామితులు.
2) తగిన షెల్ మెటీరియల్ని ఎంచుకోండి.
3) సంకోచం అసైన్మెంట్ యొక్క ఖచ్చితత్వాన్ని మెరుగుపరచడానికి గణాంక సూత్రాలకు అనుగుణంగా ఉండే సరైన పద్ధతిలో సంకోచానికి సంబంధించిన డేటాను సేకరించండి, లెక్కించండి మరియు విశ్లేషించండి.
4) పునరావృతత మరియు పునరుత్పత్తి లోపాలు పేర్కొన్న అవసరాలకు అనుగుణంగా ఉండేలా కొలత వ్యవస్థను (పరికరాలు, తనిఖీ సిబ్బంది మరియు సాంకేతికతతో సహా) తరచుగా పర్యవేక్షించండి.
5) అచ్చు డిజైన్ మరియు తయారీ స్థాయిని నిరంతరం మెరుగుపరచండి.
6) కాస్టింగ్ కరెక్షన్ మరియు స్టెబిలైజేషన్ హీట్ ట్రీట్మెంట్ వంటి చర్యలు ఇప్పటికీ చాలా సందర్భాలలో ఎంతో అవసరం
పునర్ముద్రణ కోసం దయచేసి ఈ వ్యాసం యొక్క మూలం మరియు చిరునామాను ఉంచండి: పెట్టుబడి కాస్టింగ్ యొక్క డైమెన్షనల్ స్థిరత్వాన్ని ప్రభావితం చేసే వివిధ అంశాలు
మింగే డై కాస్టింగ్ కంపెనీ నాణ్యమైన మరియు అధిక పనితీరు కలిగిన కాస్టింగ్ భాగాలు (మెటల్ డై కాస్టింగ్ భాగాల శ్రేణి ప్రధానంగా ఉన్నాయి సన్నని గోడ డై కాస్టింగ్,హాట్ ఛాంబర్ డై కాస్టింగ్,కోల్డ్ ఛాంబర్ డై కాస్టింగ్), రౌండ్ సర్వీస్ (డై కాస్టింగ్ సర్వీస్,సిఎన్సి మ్యాచింగ్,అచ్చు తయారీ, ఉపరితల చికిత్స) .ఏ కస్టమ్ అల్యూమినియం డై కాస్టింగ్, మెగ్నీషియం లేదా జమాక్ / జింక్ డై కాస్టింగ్ మరియు ఇతర కాస్టింగ్ అవసరాలు మమ్మల్ని సంప్రదించడానికి స్వాగతం.
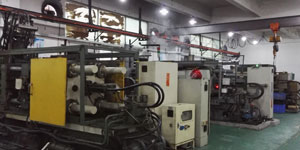
ISO9001 మరియు TS 16949 నియంత్రణలో, బ్లాస్టర్స్ నుండి అల్ట్రా సోనిక్ వాషింగ్ మెషీన్ల వరకు వందలాది అధునాతన డై కాస్టింగ్ యంత్రాలు, 5-యాక్సిస్ మెషీన్లు మరియు ఇతర సౌకర్యాల ద్వారా అన్ని ప్రక్రియలు జరుగుతాయి. మింగేకు అధునాతన పరికరాలు మాత్రమే కాకుండా ప్రొఫెషనల్ కూడా ఉన్నాయి కస్టమర్ యొక్క రూపకల్పన నిజం కావడానికి అనుభవజ్ఞులైన ఇంజనీర్లు, ఆపరేటర్లు మరియు ఇన్స్పెక్టర్ల బృందం.
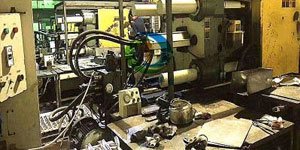
డై కాస్టింగ్ యొక్క కాంట్రాక్ట్ తయారీదారు. సామర్థ్యాలలో కోల్డ్ చాంబర్ అల్యూమినియం డై కాస్టింగ్ భాగాలు 0.15 పౌండ్లు. 6 పౌండ్లు., శీఘ్ర మార్పు ఏర్పాటు మరియు మ్యాచింగ్. విలువ-జోడించిన సేవల్లో పాలిషింగ్, వైబ్రేటింగ్, డీబరింగ్, షాట్ బ్లాస్టింగ్, పెయింటింగ్, ప్లేటింగ్, పూత, అసెంబ్లీ మరియు టూలింగ్ ఉన్నాయి. 360, 380, 383 మరియు 413 వంటి మిశ్రమాలను కలిగి ఉన్న పదార్థాలలో ఉన్నాయి.
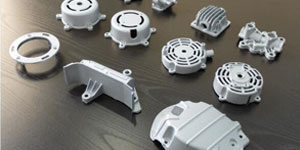
జింక్ డై కాస్టింగ్ డిజైన్ సహాయం / ఏకకాలిక ఇంజనీరింగ్ సేవలు. ఖచ్చితమైన జింక్ డై కాస్టింగ్స్ యొక్క అనుకూల తయారీదారు. సూక్ష్మ కాస్టింగ్లు, అధిక పీడన డై కాస్టింగ్లు, మల్టీ-స్లైడ్ అచ్చు కాస్టింగ్లు, సాంప్రదాయిక అచ్చు కాస్టింగ్లు, యూనిట్ డై మరియు స్వతంత్ర డై కాస్టింగ్లు మరియు కుహరం సీల్డ్ కాస్టింగ్లు తయారు చేయవచ్చు. +/- 24 in లో 0.0005 అంగుళాల వరకు పొడవు మరియు వెడల్పులలో కాస్టింగ్ తయారు చేయవచ్చు. సహనం.
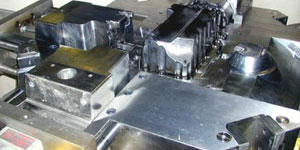
ISO 9001: 2015 డై కాస్ట్ మెగ్నీషియం యొక్క సర్టిఫైడ్ తయారీదారు, సామర్థ్యాలలో 200 టన్నుల హాట్ చాంబర్ & 3000 టన్నుల కోల్డ్ చాంబర్, టూలింగ్ డిజైన్, పాలిషింగ్, మోల్డింగ్, మ్యాచింగ్, పౌడర్ & లిక్విడ్ పెయింటింగ్, CMM సామర్థ్యాలతో పూర్తి QA , అసెంబ్లీ, ప్యాకేజింగ్ & డెలివరీ.
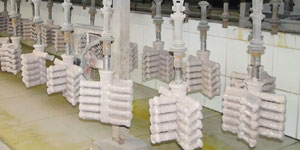
ITAF16949 ధృవీకరించబడింది. అదనపు కాస్టింగ్ సేవ చేర్చండి ఇన్వెస్ట్ కాస్టింగ్,ఇసుక తారాగణం,గ్రావిటీ కాస్టింగ్, లాస్ట్ ఫోమ్ కాస్టింగ్,సెంట్రిఫ్యూగల్ కాస్టింగ్,వాక్యూమ్ కాస్టింగ్,శాశ్వత అచ్చు కాస్టింగ్,. సామర్థ్యాలలో EDI, ఇంజనీరింగ్ సహాయం, సాలిడ్ మోడలింగ్ మరియు సెకండరీ ప్రాసెసింగ్ ఉన్నాయి.
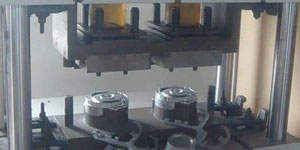
కాస్టింగ్ పరిశ్రమలు పార్ట్స్ కేస్ స్టడీస్: కార్లు, బైకులు, విమానం, సంగీత వాయిద్యాలు, వాటర్క్రాఫ్ట్, ఆప్టికల్ పరికరాలు, సెన్సార్లు, మోడల్స్, ఎలక్ట్రానిక్ పరికరాలు, ఎన్క్లోజర్స్, క్లాక్స్, మెషినరీ, ఇంజన్లు, ఫర్నిచర్, ఆభరణాలు, జిగ్స్, టెలికాం, లైటింగ్, వైద్య పరికరాలు, ఫోటోగ్రాఫిక్ పరికరాలు, రోబోట్లు, శిల్పాలు, సౌండ్ పరికరాలు, క్రీడా పరికరాలు, సాధనం, బొమ్మలు మరియు మరిన్ని.
తదుపరి చేయడానికి మేము మీకు ఏమి సహాయపడతాము?
For హోమ్ పేజీకి వెళ్ళండి డై కాస్టింగ్ చైనా
→భాగాలు ప్రసారం-మేము చేసామో తెలుసుకోండి.
→ సంబంధిత చిట్కాలు గురించి కాస్టింగ్ సేవలు చనిపోతాయి
By మింగే డై కాస్టింగ్ తయారీదారు | వర్గాలు: ఉపయోగకరమైన వ్యాసాలు |మెటీరియల్ టాగ్లు: అల్యూమినియం కాస్టింగ్, జింక్ కాస్టింగ్, మెగ్నీషియం కాస్టింగ్, టైటానియం కాస్టింగ్, స్టెయిన్లెస్ స్టీల్ కాస్టింగ్, ఇత్తడి కాస్టింగ్,కాంస్య కాస్టింగ్,వీడియో ప్రసారం,కంపెనీ చరిత్ర,అల్యూమినియం డై కాస్టింగ్ | వ్యాఖ్యలు ఆఫ్